Bowden Road – Tokyo Foods + Daikin
When you have two different warehouses on the same site with very different requirements, what do you do? Well, the first job is to give DGE a call! While it might not seem like two warehouses situated in Wiri would pose too many challenges, you haven’t seen the tenants yet! With one requiring a complex food-grade commercial fitout and one requiring state-of-the-art office facilities along with copious lighting all on a challenging site with a strict timeline – the complexity starts to ramp up. DGE were the electricians selected for the job. So, with two sites of 10,000m2 and 14,000m2, the combined intricate requirements were challenging, however, it was no problem for our team. The Challenge -20°C working conditions… no problem! Think you’ve felt the cold at work before? It was probably nothing compared to the -20°C that our team worked in for this project. However, installing a walk-in cool room and freezer to food-grade standards was just one of the challenges we faced. With two separate buildings to fit out including vastly different needs, this was a project that required depth of knowledge, careful management and a skilled team – a perfect job for DGE. This was certainly not a standard build project. The challenges began below the surface – the earthing had to be looked at in-depth as the buildings were set on volcanic soil with more rocks than dirt in some places! With both high and low voltage electrical installations to take place, this involved a complex design solution and key area to get right for this project. The next challenge was getting the equipment live – this required much communication with Vector and Northpower as specialist knowledge was necessary to connect to the existing switch gear. Then came the process of ensuring we met the specific needs of the two different clients – a food grade commercial kitchen for Tokyo Foods and a state-of-the-art office and storage warehouse for Daikin Heatpumps. As the project progressed, Daikin’s needs evolved causing changes to the working conditions, the scope of the project and the volume of lighting to be installed. Our team needed to be agile and proactive to meet those changing needs in the necessary timeframes; all while maintaining a Green Star standard build in both locations. The Scope Two warehouses, two clients, two expectations to meet This was a job with two very different stories. With two new warehouses to fit out, the two different tenants made the work quite varied. Along with this, significant solar installations were required for each building. The first building was initially untenanted, so our team began working towards a high quality Green Star standard fitout. Partway through the process, Daikin came on board as the tenant, so the scope of the job shifted to meet their needs. This included the fitout of a state-of-the-art office within the warehouse, extension of the initially installed switchboards, and triple the amount of night initially required. There was a lot of logistical planning required to accommodate and execute the modifications within the initially specified timeframe. The second building was commissioned for Tokyo Foods. Ever stepped inside a walk-in chiller and started to feel the cold instantly? Try doing that for days on end! As a commercial kitchen with a walk-in freezer unit reaching temperatures below -20°C, the scope for this job was specific and complex. The extreme temperatures within the freezer meant that we needed to source cables, conduits and fittings that could withstand the conditions and ensure everything was fed in such a way that it did not damage the interior panelling and seals of the freezer. Finally, the team had to establish that the entire system was able to be powered by a back-up generator to ensure that the precise freezing conditions could be maintained in any eventuality. The Delivery Two state-of-the-art facilities to suit complex needs When two tenants have two differing and complex electrical needs, the team on the ground needs to be skilled, proactive and organised. Three words that perfectly describe DGE. This job involved a lot – high and low voltage installations, the food-grade requirements of a commercial kitchen, extreme temperature fluctuations, agile solutions for a changing scope, and the need to meet Green Star standards and follow Green Star protocol. DGE put the gloves on and created a staged execution plan right from procurement to final completion. By communicating openly with the other contractors involved in the project and providing effective solutions, the job was completed on time and to an exceptionally high standard. The Outcome Two tenants, two needs, two sets of expectations met Despite the fact that this project involved detailed planning, significant logistics, efficient procurement of supplies, excellent communication and immense skill, DGE delivered on every requirement and exceeded two sets of client expectations. The end result was two very happy clients able to operate their businesses in an environmentally friendly way from two state-of-the-art facilities. As one of Auckland’s most highly regarded electrical engineering firms, DGE was selected for our skill and reputation. And you could choose us too! Get in touch with the team you can trust to discuss your next project.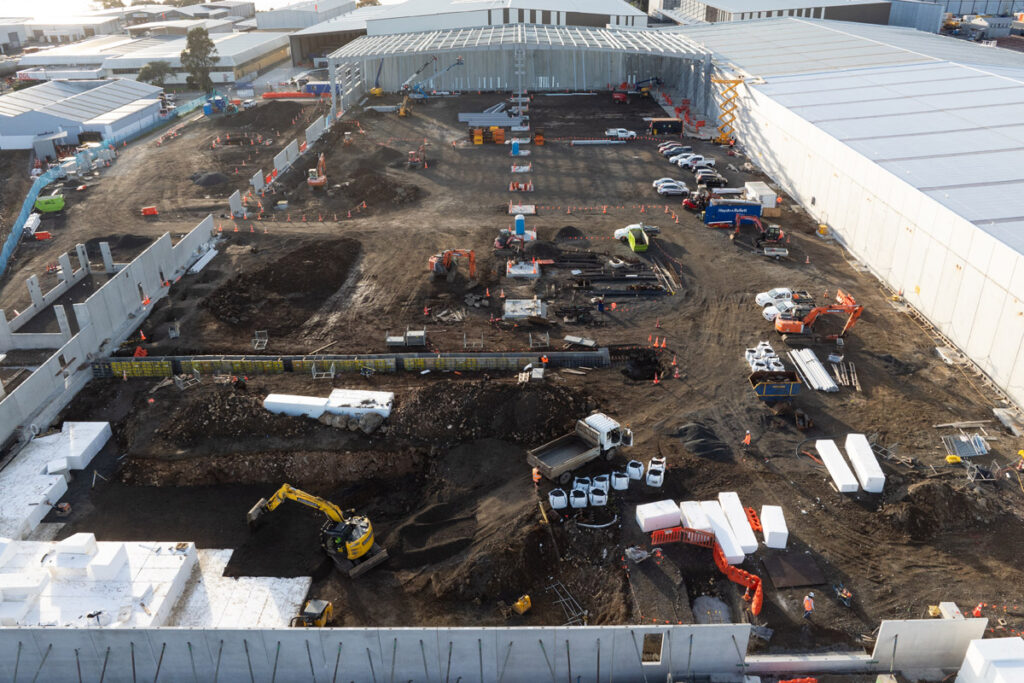
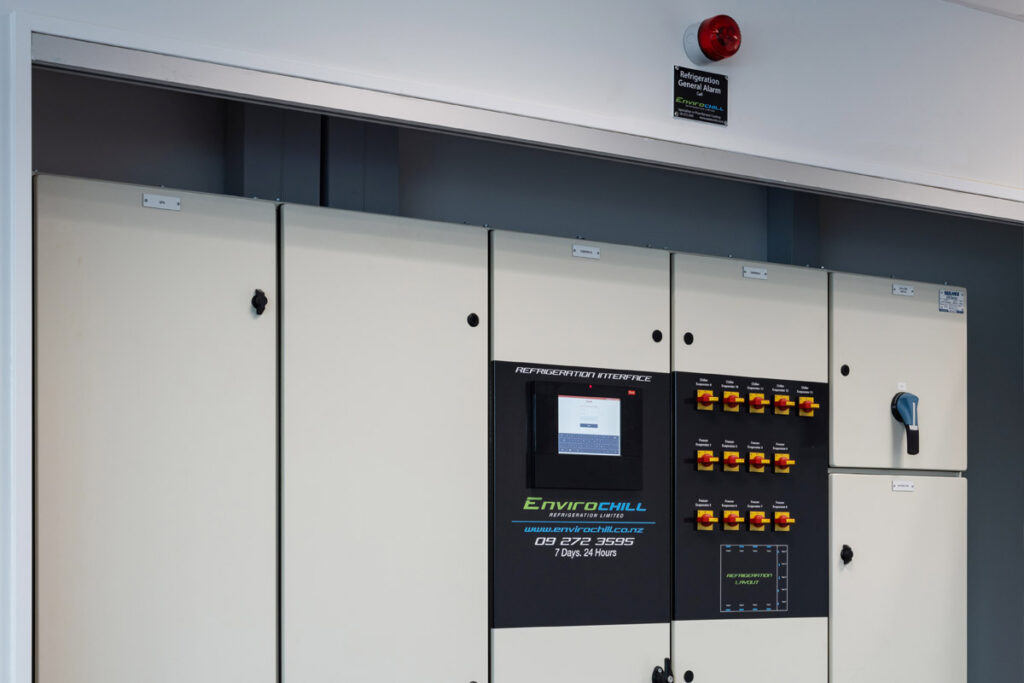
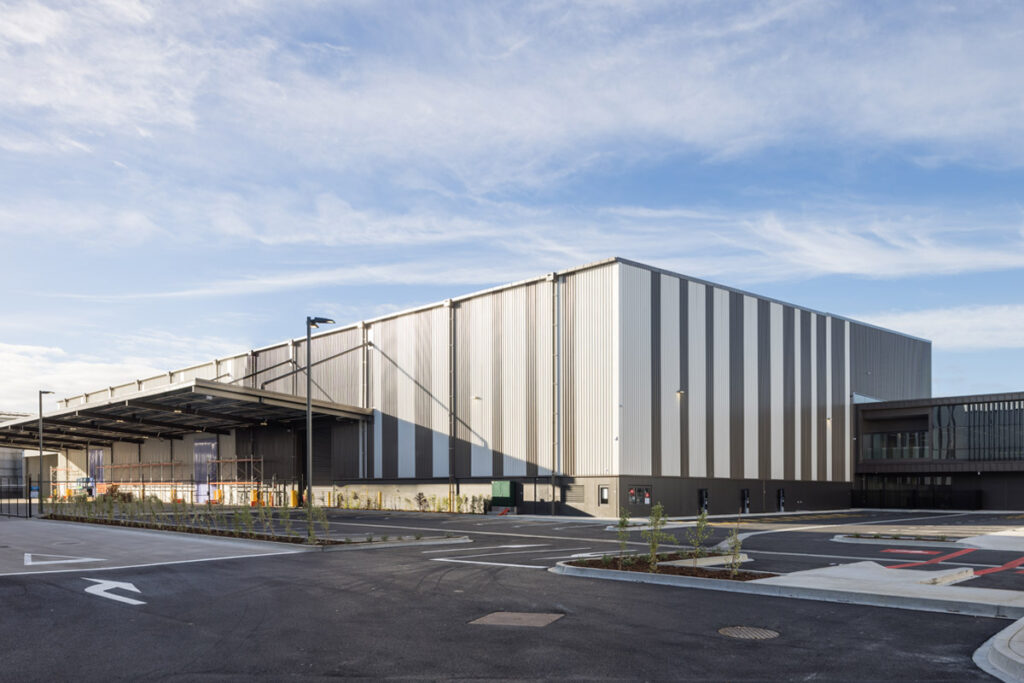
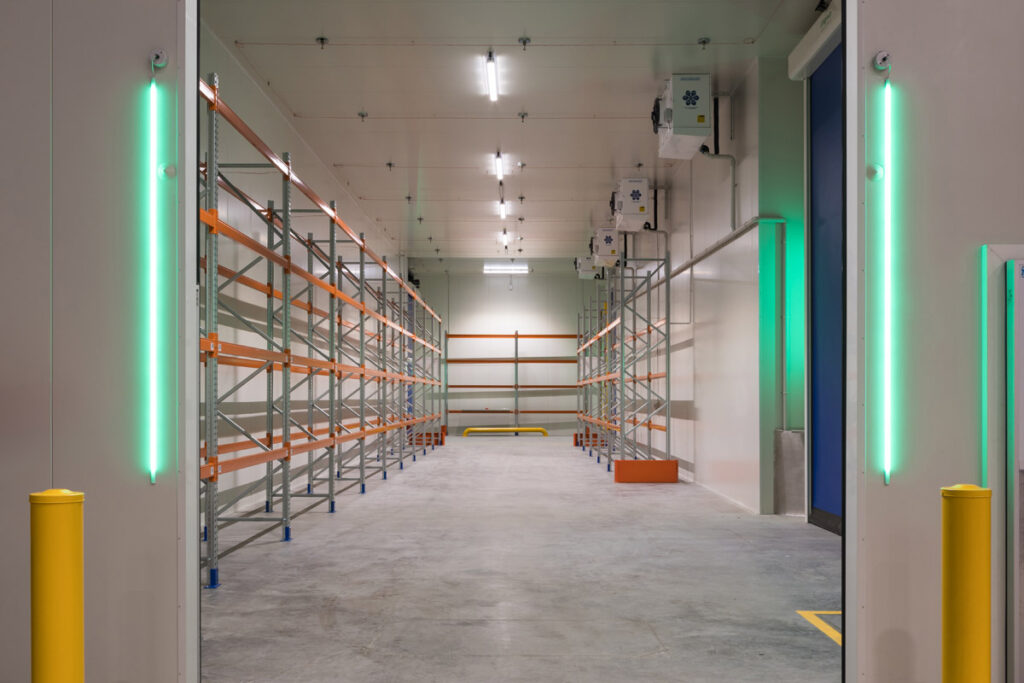
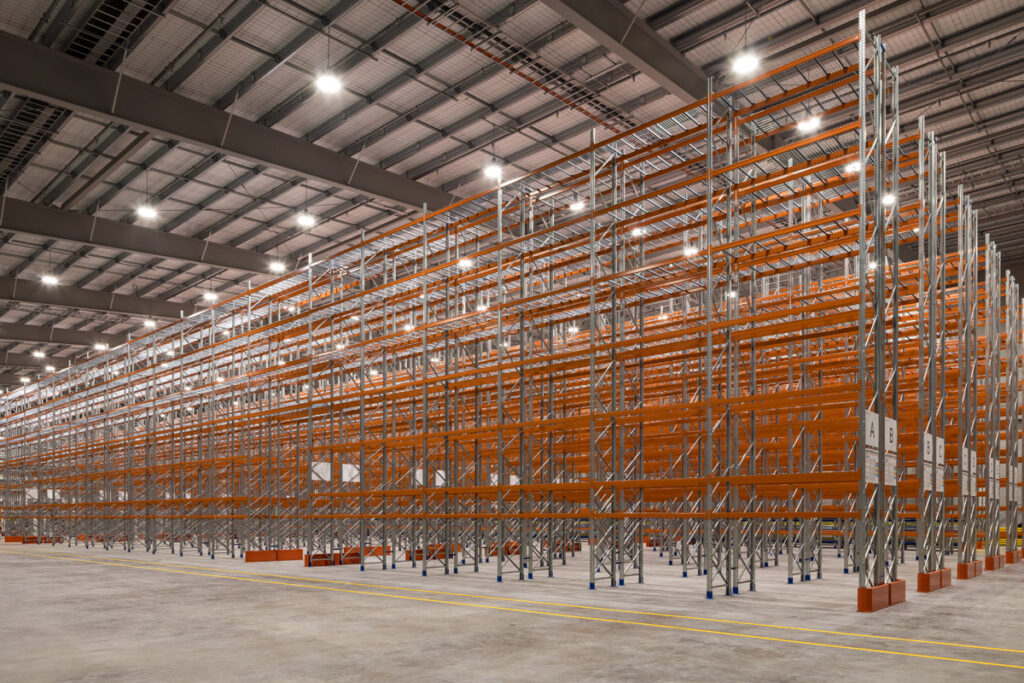
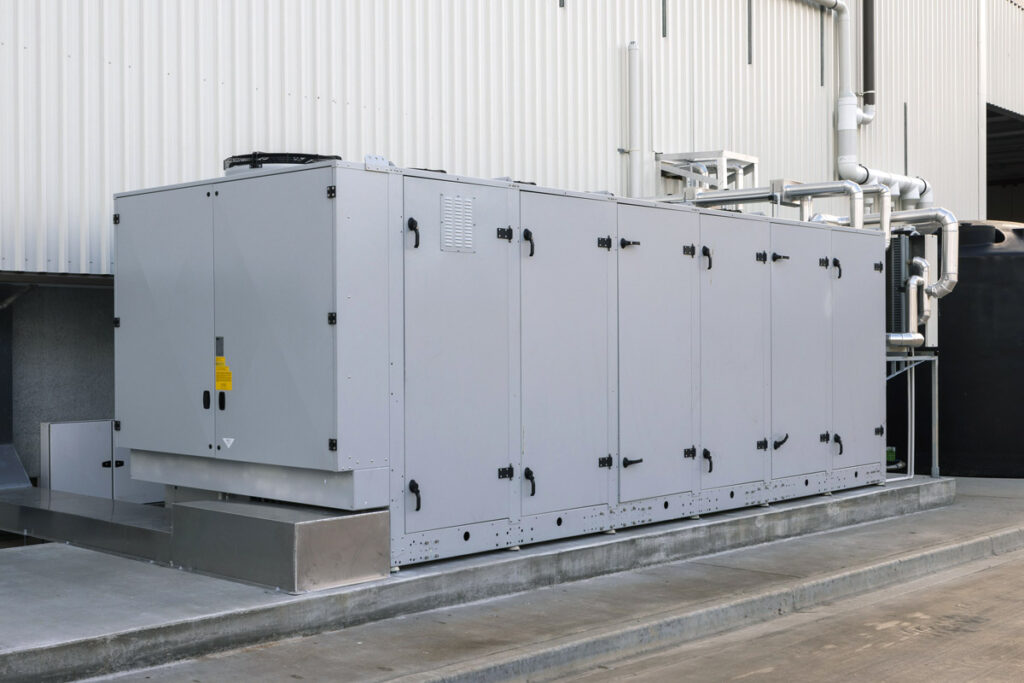
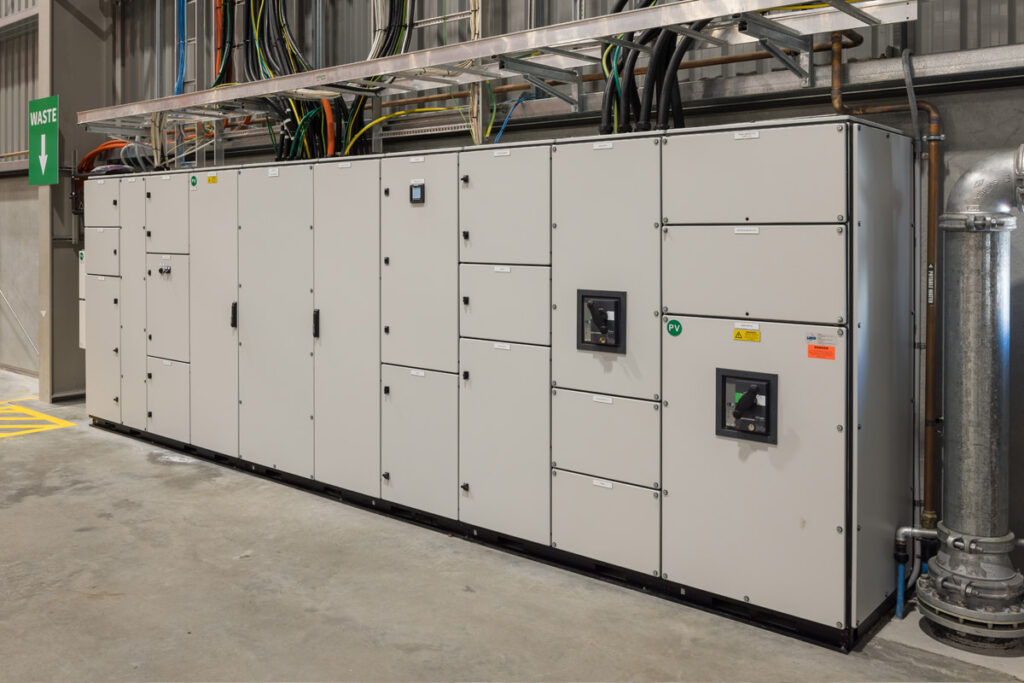
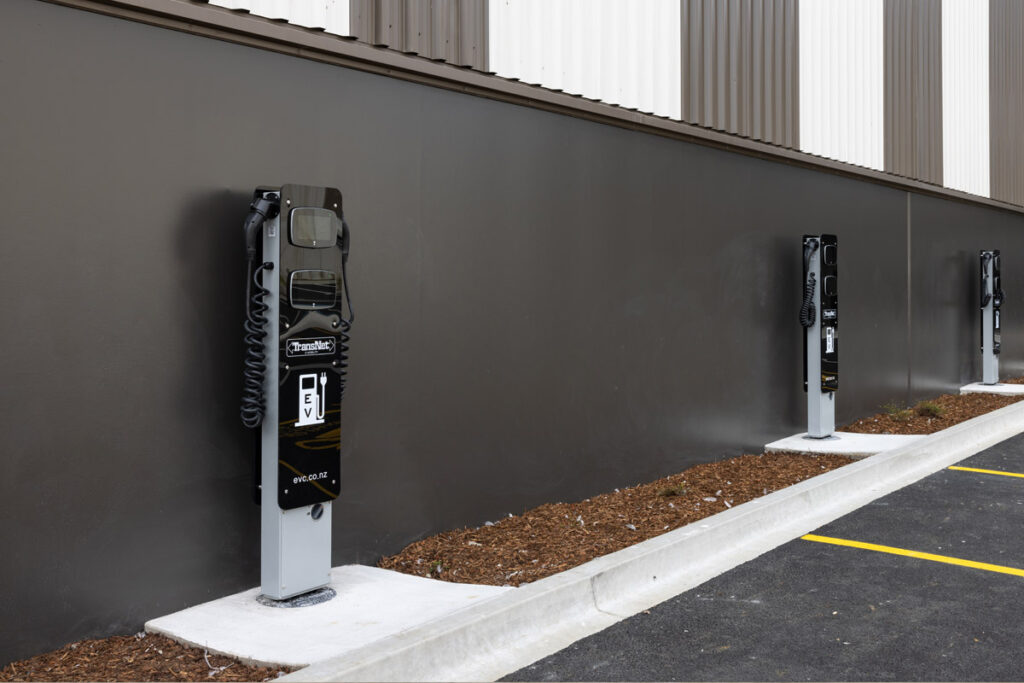